Environmental
Protection
Process integration techniques that were previously developed for energy, mass and equipment integration have now been extended to various emission and environmentally-constrained problems, taking into account footprint metrics that measure environmental impacts other than global warming.
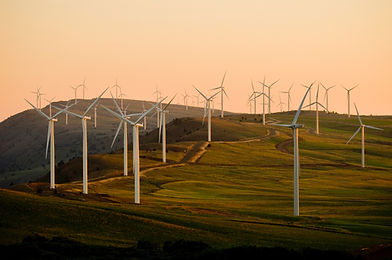
Renewable Energy Integration
According to the IPCC 5th assessment report, the industry is one of the largest energy consumers (28%) and greenhouse gas (GHG) emissions contributors worldwide (30%). Industrial actors will have to play a significant role in GHG emission reduction, both by reducing their energy intensity and their carbon footprint. Integrating Renewable Energy (RE) production assets in process industries is one means to achieve GHG emission reduction, energy conservation, and increased profitability.
​
Energy is, and will remain, a fundamental input for the industry, but new modes of energy procurement and use are technically and economically available all over the world, adapted to local contexts. RE integration in industry has already been adapted globally by a number of industrial players out of self interest. More than 200 projects were identified across all geographies, involving different industrial sectors and using an extensive array of RE technology options, from traditional ones such as rooftop solar PV to more innovative ones such as hydrogen production from a renewable source.
Different integration schemes are possible, from simple and investment - light projects to more complex, interwoven projects yielding greater reductions in energy consumption and GHG emissions.
​
-
Green power procurement with a third party power producer
-
On-site installation of fully owned and operated renewable power generation assets
-
On-site installation of RE production assets and process adaptation
RE integration in industrial processes brings direct benefits to the industrial players, such as:
​
-
Reduced energy costs and price hedging from future increases of fuel and grid prices
-
Improved energy supply reliability
-
Increased productivity
-
Additional revenue-generating opportunities
-
Greater coherence with corporate environmental and local commitments
Emission Reduction
Recent analysis by the International Energy Agency (IEA) estimated that the energy production by utilization fossil fuels accounts for about 65% of global greenhouse gas (GHG) emissions. New environmental legislation to control CO2 emissions is putting increasing pressure on the process industries. Such legislation imposes a limit on carbon emissions by industrial emitters, sets emissions reduction target, and applies economic penalties in some cases.
​
Retrofitting process plants to improve energy efficiency has proved to be a beneficial option for reducing CO2emissions. Avoiding inefficient use of energy through better operating practice or improved process design can decrease fuel consumption and hence flue gas emissions.
The retrofit of a process plant for energy savings and emission reduction can be carried out by increasing heat recovery in its heat exchanger networks (HENs) and its steam and power system, and utility system. A wide range of process design methodologies, many of which apply process integration concepts for saving energy, has been developed and successfully applied to improve the energy efficiency of existing process sites.
Some of these successful techniques that can be utilized to reduce energy consumption as well as GHG emission are:
-
Industrial Fuel Switching, omitting Flare and Incinerators, Increasing furnace and boiler operating efficiency, Etc.
-
CO2 capture processes:
-
Post Combustion Capture
-
Oxy - Fuel Combustion (process of burning a fuel using pure oxygen)
-
Pre Combustion Capture
-
Carbon Footprint
Climate change has been growing in importance to the international community. Most of the attention has been focused on the Carbon Footprint (CFP) as a measure of the extent of greenhouse gas emissions impact.
​
An interesting contribution towards pinch analysis deals with the Carbon and Footprint-Constrained Energy Planning Using Cascade Analysis Technique.
Mathematical targeting techniques have been developed for energy sector planning with CO2 emission and land availability constraints.
It is desirable to maximize the use of low carbon energy sources to reduce CO2 emissions. This technique provides an extension of the classic Pinch Analysis for identifying the minimum amount of low- or zero- carbon energy sources needed to meet the national or regional energy demand, while not violating the CO2 emission limits. Pinch Analysis can be used to study the CFP of any process industry, such as:
​
-
CFP of Chemical Processes
-
CFP of Renewable Systems
-
CFP of Electricity Generation
-
CFP of Energy Planning
Wastewater Minimization
The strive to design more cost efficient waste treatment systems inspired yet another extension of the pinch principle – the Oxygen Pinch Analysis.
The idea was to target prior to design the ideal minimum oxygen demands for micro-organisms aeration. Flowsheet and design changes were suggested based on the target.
Agitation and other forms of aeration require energy, so finally, the analysis based on oxygen pinch principles leads again to their original application associated with energy conservation.
The method also provides other indicators – quantitative targets for oxygen solubility, residence time, and oxidation energy load. In a follow-up development, a combined Water-and-Oxygen Pinch Analysis has been proposed. By combining the two criteria, up to 30 % cost savings for the wastewater treatment could be achieved.
​
Employing oxygen pinch technique can result in:
​
-
Oxygen Minimization in Waste Degradation
-
Oxygen Minimization in Wastewater Treatment
Material Conservation & Waste Minimization
The process industries are characterized by tremendous use of natural resources in the form of energy and materials. Process Integration provides an attractive framework for the design of resource conservation networks that integrate process streams and units to garner savings in energy and material usage.
Material conservation networks (MCNs) are defined as integrated systems of streams and units aimed at the enhancement of the effectiveness of mass utilization and productivity in industrial facilities as well as the protection of natural material resources.
By avoiding or reducing the production of waste, waste minimization is an effective approach to solve the pollution problem in process industries.
Process integration supported by multi-objective optimization (resulting in material conservation) provides a framework for process design or process retrofit by simultaneously optimizing on the aspects of environment and economics.
​
-
Materials Integration Within & Between Processes
-
Mass Exchanger Networks
-
Supply Chain Performance